Introduction
Diesel generators play a crucial role in providing backup power during emergencies or in areas with unreliable electricity supply. To ensure that a diesel generator operates efficiently and reliably when needed, it is important to conduct regular performance testing. bojinsi helps to identify any issues or inefficiencies in the generator system, allowing for timely maintenance and repairs. In this article, we will discuss the importance of performance testing for diesel generators and provide a comprehensive guide on how to conduct these tests effectively.
Importance of Performance Testing for Diesel Generators
Diesel generators are commonly used in various applications, such as industrial facilities, hospitals, data centers, and residential buildings. These generators are designed to provide reliable power in the event of a grid power failure or as a primary power source in off-grid locations. However, like any other mechanical equipment, diesel generators are prone to wear and tear over time. Regular performance testing is essential to ensure that the generator is operating at its optimum capacity and can provide the required power output when needed.
Performance testing helps to evaluate the overall health and efficiency of a diesel generator by measuring its key parameters, such as power output, fuel consumption, voltage regulation, and frequency stability. By conducting these tests regularly, operators can identify any issues that may affect the generator's performance and address them before they escalate into more significant problems. In addition, performance testing can help to optimize the generator's fuel efficiency, reduce emissions, and prolong its lifespan.
Types of Performance Testing for Diesel Generators
There are several types of performance testing that can be conducted on a diesel generator to assess its operational efficiency and reliability. Some of the most common tests include:
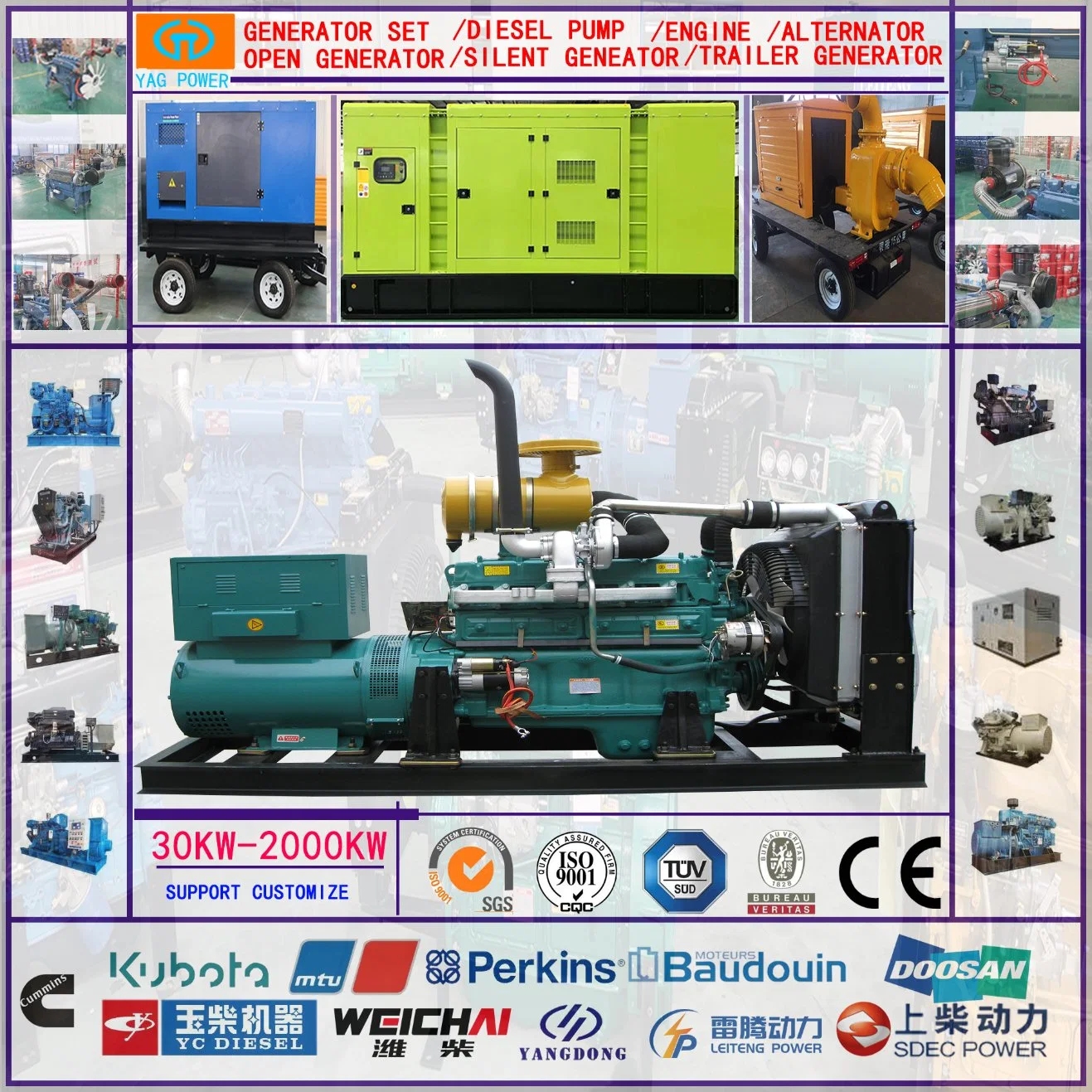
1. Load Bank Testing: Load bank testing is a crucial method for evaluating the generator's ability to handle varying loads and maintain stable voltage and frequency outputs. During load bank testing, the generator is connected to a resistive or reactive load bank that simulates the actual electrical load the generator would experience in real-world conditions. By gradually increasing the load on the generator, operators can determine its capacity to deliver the required power output without compromising its performance.
2. Fuel Consumption Testing: Fuel consumption testing involves measuring the amount of fuel consumed by the generator over a specific period of operation. This test helps to determine the generator's fuel efficiency and identify any issues that may be causing excessive fuel consumption, such as fuel leaks, clogged filters, or inefficient combustion. By monitoring fuel consumption regularly, operators can optimize the generator's fuel usage and reduce operational costs.
3. Voltage Regulation Testing: Voltage regulation testing evaluates the generator's ability to maintain a stable voltage output within acceptable limits under varying load conditions. Voltage regulation is essential to ensure that sensitive electrical equipment connected to the generator receives a consistent and reliable power supply. By testing the generator's voltage regulation capabilities, operators can identify any voltage fluctuations or irregularities and take corrective measures to address them.
4. Frequency Stability Testing: Frequency stability testing assesses the generator's ability to maintain a constant frequency output, typically 50 Hz or 60 Hz, under different load conditions. Frequency stability is critical for the proper operation of electrical equipment that relies on a specific frequency to function correctly. By testing the generator's frequency stability, operators can ensure that it meets the required frequency standards and does not cause any damage to connected devices.
5. Heat Run Testing: Heat run testing involves running the generator at full load for an extended period to evaluate its performance under high-temperature conditions. This test helps to identify any overheating issues, cooling system failures, or other thermal problems that may affect the generator's operation. Heat run testing is particularly important for diesel generators used in high-demand applications where continuous operation at full load is required.
How to Conduct Performance Testing for Diesel Generators
To conduct effective performance testing for a diesel generator, operators should follow a systematic approach and use the right tools and equipment. Here are the steps involved in conducting performance testing for diesel generators:
1. Preparation: Before conducting performance testing, operators should ensure that the generator is in good working condition and all safety precautions are in place. Inspect the generator for any signs of damage, leaks, or loose connections. Check the fuel level, oil level, coolant level, and battery condition to ensure that the generator has an adequate supply of fuel and essential fluids. Make sure that the generator is properly grounded and that all safety devices are operational.
2. Load Bank Connection: For load bank testing, connect the generator to a suitable load bank that matches the generator's capacity and voltage rating. Ensure that the load bank is properly configured to simulate the desired load profile, including resistive, inductive, and capacitive loads. Gradually increase the load on the generator while monitoring its voltage and frequency outputs to assess its performance under different load conditions.
3. Fuel Consumption Measurement: Use a fuel flow meter or fuel monitoring system to measure the amount of fuel consumed by the generator during the testing period. Record the fuel consumption data at regular intervals to calculate the generator's fuel efficiency and identify any abnormalities or variations in fuel consumption. Compare the fuel consumption data with the manufacturer's specifications to determine if the generator is operating within acceptable limits.
4. Voltage and Frequency Monitoring: Use a digital multimeter or power analyzer to monitor the generator's voltage and frequency outputs during the testing process. Measure the voltage and frequency at various load levels to assess the generator's voltage regulation and frequency stability capabilities. Ensure that the voltage and frequency outputs remain within the specified tolerances and do not fluctuate excessively under varying load conditions.
5. Thermal Monitoring: Monitor the generator's temperature levels using temperature sensors or thermal imaging cameras to detect any overheating issues during the testing process. Pay attention to the temperature of critical components such as the engine, alternator, cooling system, and exhaust system. Ensure that the generator's cooling system is functioning correctly and that the temperature levels remain within safe operating limits.
6. Data Analysis: Collect and analyze the performance data obtained during the testing process to evaluate the generator's overall efficiency and reliability. Identify any anomalies, deviations, or trends that may indicate potential problems with the generator's operation. Generate performance reports detailing the test results, including fuel consumption, voltage regulation, frequency stability, and temperature measurements.
7. Maintenance and Repairs: Based on the test results and performance analysis, schedule any necessary maintenance or repairs to address identified issues and ensure that the generator is operating at its optimum capacity. Replace worn-out parts, clean filters, adjust settings, or recalibrate components as needed to improve the generator's performance and efficiency. Keep detailed records of all maintenance activities and performance test results for future reference.
Conclusion
Performance testing is a critical aspect of diesel generator maintenance and operation, as it helps to ensure that the generator can deliver reliable power output when needed. By conducting regular performance tests, operators can identify and address any issues that may affect the generator's efficiency, reliability, and longevity. Load bank testing, fuel consumption testing, voltage regulation testing, frequency stability testing, and heat run testing are essential methods for evaluating the performance of a diesel generator under various operating conditions. By following a systematic approach and using the right tools and equipment, operators can optimize the performance of their diesel generators and minimize the risk of unexpected failures or downtime.